1. Fundamental Principles of CO2 Laser Cutting Technology
CO2 laser cutting technology operates on the principles of focused high-intensity light. A mixture of carbon dioxide, nitrogen, and helium gases is excited electrically, producing a laser beam at a wavelength of around 10.6 micrometers. This wavelength is highly absorbed by most materials, making it an effective cutting tool. The laser beam is focused onto the workpiece using precision optics, resulting in localized heating and vaporization. The focused energy causes a controlled separation in the material, creating precise cuts with minimal heat-affected zones.
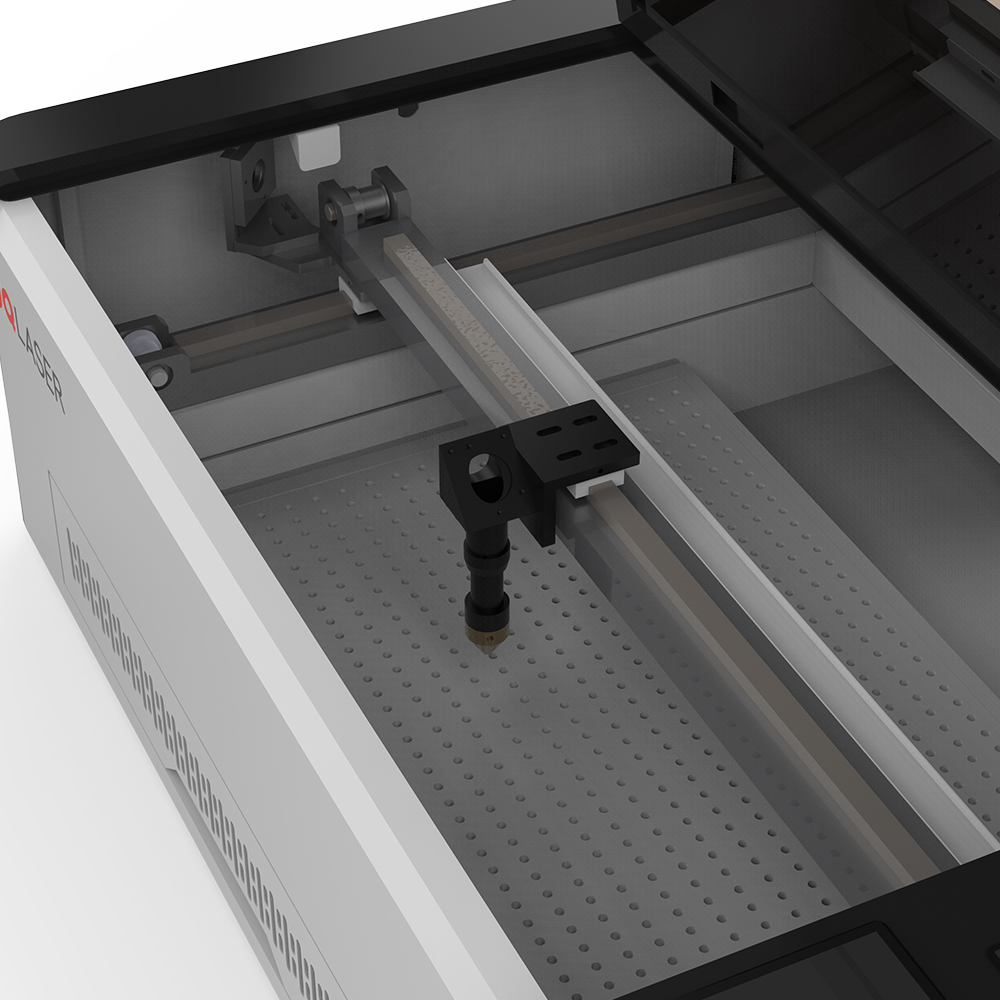
2. Material Diversity: Applications of CO2 Laser Cutting on Various Materials
CO2 laser cutting exhibits remarkable versatility, accommodating a wide range of materials. It excels in cutting metals, such as stainless steel, aluminum, and carbon steel, due to their high absorption of the 10.6 μm wavelength. Additionally, the technology proves effective on non-metals like wood, acrylic, textiles, and plastics. This adaptability has found applications in industries spanning automotive, aerospace, electronics, signage, and beyond.
3. High Precision and Micro Features: Fine Processing Capabilities of CO2 Laser Cutting
CO2 laser cutting’s precision is unmatched, with the ability to achieve intricate cuts and micro features. The focused laser beam can achieve spot sizes as small as 0.1mm, enabling detailed designs and small-scale components. This capability is especially advantageous in industries like electronics, where miniaturization is a key trend, and in producing complex patterns for decorative and functional purposes.
4. Role in Industrial Revolution: Applications of CO2 Laser Cutting in Mass Production
CO2 laser cutting has played a pivotal role in the modern industrial revolution. Its speed, accuracy, and repeatability have made it a cornerstone of mass production processes. In the automotive sector, for instance, CO2 laser cutting machines precisely shape automotive components with speed, ensuring consistent quality across production runs.
5. Driving Innovative Design: Possibilities of CO2 Laser Cutting in Product Design
The flexibility of CO2 laser cutting encourages innovative product design. Designers can explore intricate patterns, interlocking components, and unique textures that were once unattainable with conventional cutting methods. This has revolutionized architecture, interior design, and consumer product industries, enabling the creation of distinctive and functional designs.
6. Optical System Optimization: Beam Delivery and Focusing Techniques in CO2 Laser Cutting Machines
The precision of CO2 laser cutting heavily relies on sophisticated optical systems. Mirrors and lenses direct the laser beam to the workpiece while focusing it to a precise spot. These optics are meticulously aligned and calibrated to ensure consistent energy delivery. The constant advancements in beam delivery and focusing techniques enhance cutting accuracy and efficiency.
7. Choice for Eco-Friendly Manufacturing: Waste-Free Processing Advantages of CO2 Laser Cutting
CO2 laser cutting is synonymous with environmentally friendly manufacturing due to its waste-free processing. Unlike traditional methods that generate chips, shavings, or abrasive dust, laser cutting creates minimal waste. The localized heating and vaporization leave behind only a narrow kerf, optimizing material utilization and minimizing environmental impact.
8. Automation and Intelligence: Integration of CO2 Laser Cutting Systems into Production Lines
Automation has transformed manufacturing, and CO2 laser cutting systems are no exception. These systems are easily integrated into automated production lines, enabling continuous and uninterrupted processing. Moreover, advanced software controls facilitate real-time adjustments, material tracking, and remote monitoring, ensuring optimized production workflows.
9. Challenges and Solutions in CO2 Laser Cutting
While CO2 laser cutting offers numerous benefits, challenges do arise. High reflectivity materials like aluminum can cause energy loss, demanding specific strategies to enhance absorption. Controlling heat distribution to prevent warping in thin materials also requires careful consideration. Solutions involve adjusting laser parameters, employing assist gases, and refining the optical setup to ensure consistent results.
10. Future Outlook: Continuous Innovation and Development in CO2 Laser Cutting Technology
The trajectory of CO2 laser cutting technology remains promising. Ongoing research focuses on refining beam quality, optimizing energy efficiency, and expanding material capabilities. Integration with Industry 4.0 principles, such as AI-driven process optimization and predictive maintenance, will further enhance the technology’s role in modern manufacturing. As industry demands evolve, CO2 laser cutting’s adaptability and precision will continue to reshape the manufacturing landscape.