Laser welding is a highly efficient process that employs a concentrated laser beam to fuse two or more materials together, creating a strong, durable joint. This technique has gained popularity across various industries due to its ability to produce high-quality welds with minimal thermal distortion. The fundamental principle behind laser welding involves melting the edges of the materials being joined, allowing them to flow together as they cool, forming a solid bond.In laser welding, different types of lasers can be utilized, including CO2 lasers and Nd:YAG lasers, each offering unique advantages depending on the materials and thicknesses involved. CO2 lasers are particularly effective for joining thicker materials, while Nd:YAG lasers excel in applications requiring precision on smaller components. The process is characterized by its speed and efficiency, making it ideal for high-volume production environments where time is critical.
Advantages of Laser Welding
- High Speed: One of the most significant advantages of laser welding is its rapid processing capability. The speed at which welds can be completed not only increases productivity but also reduces overall manufacturing costs.
- Minimal Heat Affected Zone: Laser welding produces a smaller heat affected zone (HAZ) compared to traditional welding methods. This characteristic minimizes the risk of warping or damaging surrounding material, which is particularly important in sensitive applications.
- Versatility: Laser welding can be applied to a wide range of materials, including metals and some plastics, making it suitable for various industries such as automotive, aerospace, and electronics.
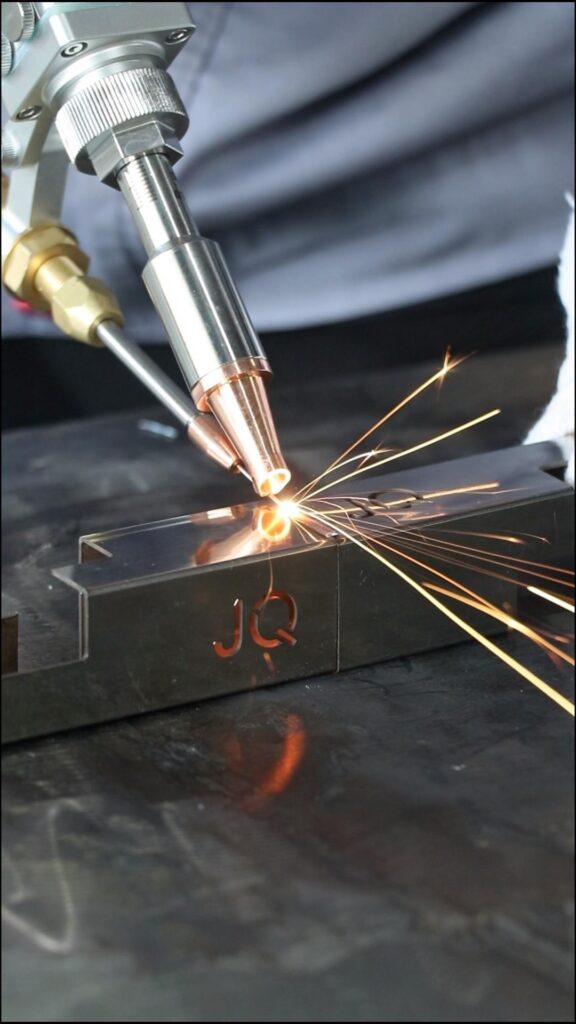
Applications of Laser Welding
Laser welding is utilized in numerous applications, including:
- Automotive Industry: Joining components in vehicles requires strong and reliable welds. Laser welding allows for precise connections that enhance structural integrity while reducing weight.
- Aerospace: In aerospace applications, where safety and performance are paramount, laser welding provides the necessary strength without adding excessive weight.
- Electronics: The ability to create small, precise welds makes laser welding ideal for assembling delicate electronic components.
Exploring Laser Cladding Technology
Laser cladding is an advanced technique that involves depositing material onto a substrate using a laser beam. Unlike laser welding, which fuses materials together, laser cladding creates a metallurgical bond between a coating material (often in powder form) and the substrate surface. This process enhances surface properties such as wear resistance, corrosion resistance, and overall durability.During laser cladding, the laser energy melts both the substrate surface and the coating material simultaneously. As these materials cool together, they form a strong bond that can significantly improve the performance characteristics of the component. This method is particularly valuable for repairing worn parts or enhancing existing components without compromising their structural integrity.
Benefits of Laser Cladding
- Enhanced Surface Properties: One of the primary advantages of laser cladding is its ability to improve surface characteristics such as hardness and resistance to wear or corrosion. This enhancement extends the lifespan of components subjected to harsh operating conditions.
- Low Heat Input: The localized heating during laser cladding minimizes thermal distortion and damage to the underlying substrate. This feature is crucial when working with sensitive materials that could be adversely affected by excessive heat.
- Material Versatility: Various materials can be used for cladding, including ferrous alloys, non-ferrous metals, and even specialized coatings designed for specific applications. This versatility allows engineers to tailor solutions based on performance requirements.
Applications of Laser Cladding
Laser cladding finds applications in several industries:
- Oil & Gas: In this sector, laser cladding is used to repair drilling equipment and enhance components exposed to extreme conditions.
- Aerospace: Components such as turbine blades benefit from laser cladding due to improved wear resistance and extended service life.
- Manufacturing: Repairing molds or tooling through laser cladding helps manufacturers reduce costs associated with replacing expensive equipment.
Key Differences Between Laser Welding and Laser Cladding
While both laser welding and laser cladding utilize lasers for processing materials, they serve distinct purposes within manufacturing:
Feature | Laser Welding | Laser Cladding |
---|---|---|
Purpose | Fuse two or more materials | Deposit material onto surfaces |
Process Type | Material joining | Additive manufacturing |
Filler Material | Not required | Required (usually in powder form) |
Heat Affected Zone | Minimal heat affected zone | Limited heat affected zone |
Material Types | Metals (various types) | Primarily metals and alloys |
Precision | High precision joints | High precision deposits |
Application Focus | Creating strong joints | Enhancing surface properties |
Understanding these differences is crucial for manufacturers when selecting the appropriate technology for their specific needs. Each method offers unique advantages that cater to different aspects of production processes.
The Synergy Between Machining and Laser Technologies
Machining is a traditional manufacturing process that involves removing material from a workpiece to achieve desired shapes and dimensions. When combined with laser technologies such as welding or cladding, machining enhances effectiveness by providing clean surfaces for either joining or coating applications.
Benefits of Combining Machining with Laser Technologies
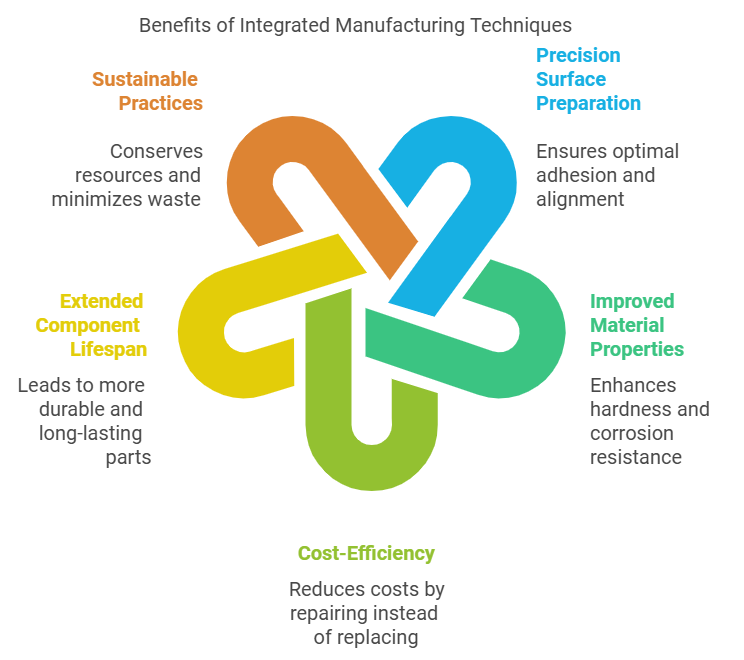
- Precision Surface Preparation: Machining ensures surfaces are properly contoured for optimal adhesion during cladding or precise alignment during welding processes. This preparation enhances overall quality and performance.
- Improved Material Properties: By removing degraded material before applying coatings or performing welds, manufacturers can achieve improved characteristics such as higher hardness or better corrosion resistance in finished products.
- Cost-Efficiency: This integrated approach reduces material costs by focusing on repairing rather than replacing entire components. Manufacturers can save significantly by extending the life cycle of existing parts rather than investing in new ones.
- Extended Component Lifespan: The combination leads to more durable components that require less frequent maintenance or replacement over time. This longevity translates into lower operational costs throughout a component’s lifecycle.
- Sustainable Practices: Refurbishing existing components helps conserve resources by reducing the need for new materials while minimizing waste generation during production processes.
Comparing Cost Factors in Laser Technologies
When evaluating laser welding versus laser cladding from a cost perspective, several factors must be considered:
Initial Investment
Both technologies require significant initial investments in equipment; however, laser cladding systems tend to be more expensive due to their complexity and precision requirements compared to traditional welding machines.
Operational Costs
Operational costs can vary based on energy consumption, maintenance needs, and labor requirements:
- Laser Welding:
- Generally lower operational costs due to faster processing times compared to other methods.
- Higher energy consumption when working with thicker materials may offset initial savings if not managed properly.
- Laser Cladding:
- More energy-efficient due to automated processes that optimize resource usage.
- Requires skilled operators leading to potentially higher labor costs; however, this investment pays off through improved quality control.
Long-Term Savings
Both technologies offer long-term savings through reduced material waste and enhanced product quality:
- Reducing defects leads to fewer reworks or replacements over time.
- Improved durability extends product lifespans, lowering overall production costs as fewer replacements are needed throughout a component’s lifecycle.
Future Trends in Laser Technologies
As industries continue to evolve, so do the technologies associated with laser welding and cladding. Emerging trends include:
- Automation Integration: Increased automation will streamline processes in both laser cutting and cladding applications by minimizing human error while maximizing efficiency through advanced robotics systems.
- Advanced Materials: Research into new alloys and composite materials will expand capabilities; this innovation enables manufacturers to explore new applications previously deemed impractical due to material limitations.
- Sustainability Focus: As environmental concerns grow among consumers and regulators alike, manufacturers will seek processes that minimize waste generation while optimizing energy consumption throughout production cycles.
- Enhanced Software Solutions: Improved software for design modeling will optimize both processes for better efficiency; these advancements allow engineers greater flexibility when designing complex geometries suited specifically toward either method’s strengths.
- Hybrid Technologies: The combination of different manufacturing processes may lead to innovative solutions that leverage strengths from both laser cutting techniques alongside additive approaches like those found within traditional welding practices—ultimately enhancing overall productivity levels across multiple sectors involved within engineering disciplines today!
Conclusion on Choosing Between Technologies
When deciding between laser welding and laser cladding technologies it is essential consider specific project requirements such as material types desired outcomes cost implications operational capabilities involved each method offers unique advantages cater different aspects manufacturing—from creating intricate parts through precise cuts enhancing component durability via effective surface treatments understanding these differences comprehensively allows manufacturers make informed decisions align production goals maximizing efficiency quality across operations!