CO2 lasers are widely used in industrial manufacturing for cutting, welding, and surface treatment of materials. Optimizing the use of CO2 lasers can significantly improve productivity, cut quality, and operational efficiency. This article explores key strategies and techniques to get the most out of your CO2 laser system.Laser Beam Quality and PowerThe foundation of CO2 laser optimization lies in maintaining excellent beam quality and consistent power output. Regular maintenance of the laser resonator, optics, and cooling system is crucial. Clean or replace mirrors and lenses as needed to prevent power loss and beam distortion. Monitor and adjust gas mixture ratios to ensure optimal lasing conditions. Implementing a beam analysis system can help track beam parameters over time and identify when adjustments are needed.
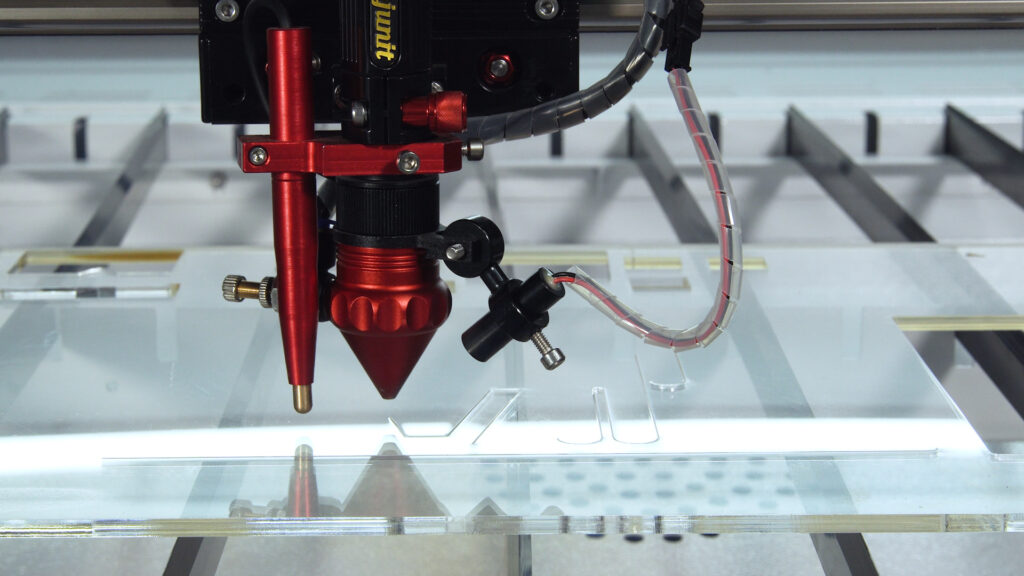
CO2 Laser Optimization Quick Facts | |
---|---|
Key Parameters | Power, focal length, assist gas, cutting speed |
Maintenance Frequency | Daily, weekly, and monthly checks recommended |
Typical Power Range | 1,000 to 6,000 watts for industrial applications |
Common Materials | Metals, plastics, wood, textiles, paper |
Beam Mode | TEM00 (Gaussian) preferred for most applications |
Reference Standard | ISO 11146 for beam parameter measurements |
Source: Laser Institute of America (www.lia.org)
Material-Specific Optimization
Different materials require tailored laser parameters for optimal processing. For metals, use oxygen as an assist gas for exothermic cutting of mild steel, while nitrogen works better for stainless steel and aluminum to prevent oxidation. When cutting plastics, reduce power and increase speed to minimize melting and achieve clean edges. For organic materials like wood or textiles, use air assist to cool the cut zone and prevent charring.Create a database of optimized parameters for commonly processed materials and thicknesses. This allows operators to quickly set up jobs with proven settings, reducing trial and error time. Regularly update this database as you discover improved parameters through experimentation or feedback from production runs.
Focus and Nozzle Optimization
Proper focal length and nozzle configuration are critical for achieving high-quality cuts. Use a shorter focal length lens for thinner materials to achieve a smaller kerf width and higher energy density. For thicker materials, a longer focal length provides better edge quality and reduces dross formation. Experiment with different nozzle designs and standoff distances to optimize gas flow dynamics and debris removal from the cut zone.Implement an auto-focus system to maintain consistent focal position, especially when processing materials with varying thicknesses or warpage. This ensures optimal energy delivery to the workpiece throughout the cutting process. For complex parts, consider using a height sensor to dynamically adjust the focal position based on surface variations.
Cutting Path Optimization
Efficient cutting paths can significantly reduce processing time and improve part quality. Use nesting software to optimize material utilization and minimize rapid traverses between cuts. Implement lead-ins and lead-outs appropriate for each material and thickness to achieve clean start and end points. For internal features, use a “tabbed” cutting approach to prevent parts from tipping up and potentially causing collisions.When cutting thick materials, consider using a multi-pass cutting strategy. This involves making several passes at progressively lower depths, allowing for better heat dissipation and improved edge quality. For intricate parts, use corner ramping techniques to maintain consistent cutting speed around sharp turns, preventing overheating and potential burn-through.
Assist Gas Management
Proper assist gas management is crucial for achieving clean cuts and extending consumable life. Use high-purity gases (99.999% or better) to prevent contamination and ensure consistent cutting performance. Implement a gas delivery system with adequate pressure and flow capacity to maintain stable gas conditions at the nozzle. For oxygen cutting of thick mild steel, consider using a coaxial oxygen jet to enhance the exothermic reaction and improve cut speed. Experiment with different gas pressures and flow rates to find the optimal balance between cut quality and gas consumption. In some cases, using a lower gas pressure with a larger nozzle orifice can achieve similar results while reducing overall gas usage. For non-metal cutting applications, consider using compressed air instead of nitrogen to reduce operating costs.
Power and Speed Optimization
Finding the right balance between laser power and cutting speed is essential for maximizing productivity while maintaining cut quality. Generally, increase power and speed proportionally to maintain consistent energy input per unit length. However, be aware that excessively high speeds can lead to striations or incomplete cutting, while too much power can cause excessive melting or burning.Implement a cut quality monitoring system to provide real-time feedback on cut performance. This can help operators quickly identify and correct issues related to power and speed settings. For production environments, consider using adaptive control systems that automatically adjust power and speed based on material variations or changing cut conditions.Thermal ManagementEffective thermal management is crucial for maintaining consistent cutting performance and extending the life of laser components. Ensure that the chiller system is properly sized for your laser’s heat load and ambient conditions. Regularly clean or replace coolant filters and maintain proper coolant chemistry to prevent scaling and corrosion.For high-duty cycle applications, consider implementing additional cooling measures such as air knives or mist cooling systems to prevent workpiece overheating. This is particularly important when cutting heat-sensitive materials or processing parts with tight tolerances.
Beam Delivery System Optimization
The beam delivery system, including mirrors, lenses, and beam path, plays a critical role in maintaining beam quality from the resonator to the workpiece. Regularly inspect and clean all optical components to prevent power loss and beam distortion. Use high-reflectivity mirrors and anti-reflection coated lenses to maximize power transmission.Implement a beam alignment verification system to ensure consistent beam positioning, especially after maintenance or lens changes. For systems with long beam paths, consider using beam stabilization technology to compensate for thermal drift and vibration effects.
Process Monitoring and Data Analysis
Implementing comprehensive process monitoring and data analysis can provide valuable insights for continuous optimization. Use sensors to track key parameters such as power output, beam characteristics, assist gas pressure, and cutting speed. Collect and analyze this data to identify trends, predict maintenance needs, and optimize cutting parameters over time.Consider implementing machine learning algorithms to analyze large datasets and identify complex relationships between process parameters and cut quality. This can lead to more sophisticated optimization strategies and potentially uncover non-intuitive parameter combinations that yield superior results.
Operator Training and Standard Operating Procedures
Well-trained operators are essential for maintaining optimal CO2 laser performance. Develop comprehensive training programs that cover not only basic operation but also troubleshooting, maintenance, and optimization techniques. Create detailed standard operating procedures (SOPs) for common tasks and parameter adjustments to ensure consistency across shifts and operators.Encourage a culture of continuous improvement by implementing a system for operators to share insights and best practices. Regularly review and update SOPs based on production data and operator feedback to incorporate new optimization strategies as they are discovered.By implementing these optimization strategies, manufacturers can significantly enhance the performance and efficiency of their CO2 laser systems. Regular evaluation and refinement of these techniques will ensure that your laser cutting operations remain at the cutting edge of productivity and quality.
CO2 laser cutting machine promotion
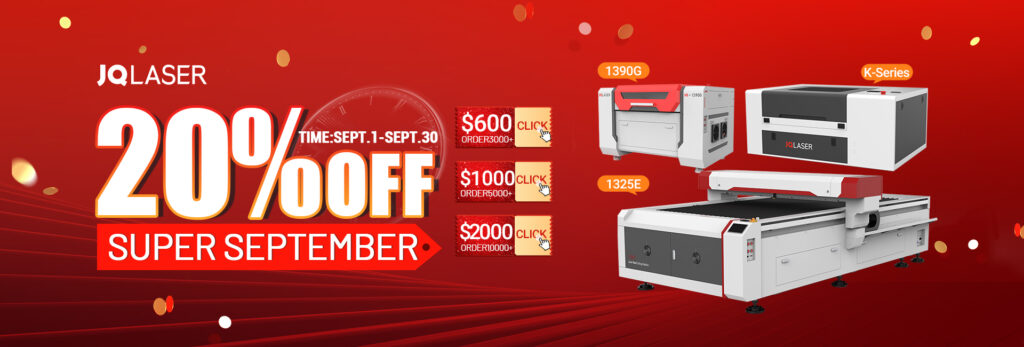