Acrylic is a widely used thermoplastic known for its optical clarity and versatility in various applications, from signage to intricate designs. The CO2 laser cutting machine is particularly effective for cutting acrylic due to its ability to produce smooth, clean edges with minimal post-processing required. However, several factors can significantly affect the cutting quality and efficiency of these machines. Understanding these factors is crucial for anyone looking to optimize their laser cutting processes and achieve the best possible results.
Material Type
The type of acrylic being cut plays a significant role in determining the effectiveness of a CO2 laser cutter. Acrylic comes in two primary forms: cast and extruded. Cast acrylic is generally preferred for applications that require engraving due to its ability to withstand heat without cracking or warping. This property allows for intricate designs and detailed engravings without compromising the material’s integrity. On the other hand, extruded acrylic is more suitable for cutting applications because it tends to provide smoother edges and better clarity after being cut. The differences between these two types of acrylic can impact not only the aesthetic quality of the finished product but also the efficiency and speed of the cutting process.
- Cast Acrylic: This type is often used in applications where clarity and detail are paramount, such as in display cases or artistic installations. Its resistance to cracking makes it ideal for more delicate work.
- Extruded Acrylic: Typically used in signage or larger projects, this material is easier to cut and can be produced in larger sheets, making it a popular choice for industrial applications.
Understanding the specific characteristics of each type of acrylic allows operators to select the most appropriate material for their projects, thereby enhancing both efficiency and output quality.
Laser Power Settings
The power setting on a CO2 laser cutter is critical in achieving optimal results when cutting acrylic. The general guideline suggests using approximately 10 watts of laser power for every millimeter of material thickness. This means that if you are working with a 10mm thick sheet of acrylic, you would typically require around 100 watts of power. However, this is not a one-size-fits-all rule; various factors such as the type of acrylic, desired cut quality, and machine capabilities can necessitate adjustments to these settings.
- Power Recommendations:
- For 1mm thickness: A power setting of around 10W is usually sufficient.
- For 5mm thickness: Increasing the power to about 50W will ensure a clean cut.
- For 10mm thickness: A power setting closer to 100W may be required to penetrate adequately without excessive melting.
Adjusting the power settings according to material thickness ensures that the laser penetrates adequately without causing excessive melting or burning. Moreover, understanding how different materials react to varying power levels can help operators fine-tune their settings for optimal performance.
Cutting Speed
Cutting speed must be carefully calibrated to match both the power settings and material thickness. Faster speeds may be suitable for thinner materials, while thicker acrylic sheets require slower speeds to ensure clean cuts without rough edges or burn marks. The relationship between speed and power is crucial; if the speed is too high relative to the power being applied, it can lead to incomplete cuts or poor edge quality.
- Speed Recommendations:
- For thinner materials (1-3mm): Higher speeds (e.g., 20-30 mm/s) are often effective.
- For thicker materials (5-10mm): Slower speeds (e.g., 10-15 mm/s) may be necessary to achieve clean cuts.
Finding the right balance between speed and power is essential for achieving optimal cut quality. Operators should conduct tests on scrap pieces before starting on final products to determine the best combination of speed and power settings based on their specific materials.
Focus Position
The focus position of the laser beam directly affects the quality of the cut. A well-focused beam ensures that energy is concentrated effectively on the material, resulting in cleaner cuts with reduced kerf width—the width of material removed during cutting. An improperly focused beam can lead to issues such as excessive melting, charring, or incomplete cuts, which can compromise both aesthetics and structural integrity.
- Focus Adjustment Tips:
- Regularly check and adjust focus settings based on material thickness; this may involve changing lenses or adjusting machine settings.
- Use focal lenses appropriate for acrylic cutting; specialized lenses can improve focus quality and enhance cutting precision.
Proper focus adjustment not only improves cut quality but also increases operational efficiency by reducing waste and minimizing rework on poorly cut pieces.
Auxiliary Gas Pressure
The use of auxiliary gases during the cutting process can enhance cut quality by blowing away melted material and preventing slag from adhering to the cut edge. Compressed air or inert gases like nitrogen are commonly used, with pressure adjustments based on material thickness. The right gas pressure helps maintain a clean cutting area by removing debris that could interfere with the laser’s effectiveness.
- Gas Recommendations:
- For thin materials: Higher gas pressure can help clear away molten debris quickly.
- For thicker materials: Lower gas pressure may be more effective in preventing excessive blow-back that could affect edge quality.
Maintaining optimal gas pressure helps ensure smooth cuts while preventing damage to both the workpiece and the machine itself. Operators should experiment with different gas types and pressures to find what works best for their specific applications.
Additional Considerations
Reflectivity of Material Surface
The surface properties of acrylic can impact how well it absorbs laser energy. A clean, smooth surface will absorb more light than a rough or dirty one, which can lead to better cutting performance. Any contaminants on the surface—like dust or grease—can scatter laser energy, resulting in uneven cuts or increased wear on the machine’s components.
- Ensure that acrylic sheets are free from dust or contaminants before cutting; regular cleaning protocols should be established as part of routine maintenance.
By taking care of surface preparation, operators can significantly improve both cut quality and machine longevity while reducing operational costs associated with rework or equipment repairs.
Nozzle Diameter
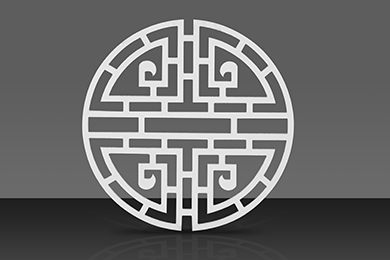
The diameter of the nozzle used in conjunction with the laser cutter affects beam focus and airflow during cutting. Smaller nozzles provide concentrated airflow, which helps clear debris from cuts and improves overall quality by reducing heat buildup around the cut area. Conversely, larger nozzles may disperse air too widely, leading to less effective debris removal.
- Use a truncated nozzle with a small diameter output for best results; this configuration allows for better control over airflow while maintaining precision in beam focus.
Choosing the right nozzle size is an often-overlooked aspect that can have a significant impact on overall cutting performance and efficiency.
Summary Table
Factor | Description |
---|---|
Material Type | Cast vs Extruded |
Laser Power | Recommended wattage based on thickness |
Cutting Speed | Adjustments needed based on material thickness |
Focus Position | Importance of proper focus adjustment |
Auxiliary Gas Pressure | Effects on cut quality based on gas type and pressure |
Reflectivity | Impact of surface cleanliness on absorption rates |
Nozzle Diameter | Influence on beam focus and airflow |
These factors collectively contribute to achieving high-quality cuts when using a CO2 laser cutting machine on acrylic materials. By understanding and optimizing these variables, operators can enhance their cutting processes, reduce waste, and achieve superior results in their projects.For further reading on this topic, you may refer to resources like Xometry’s guide on acrylic laser cutting, which provides additional insights into techniques and best practices specific to this process. This expanded article delves deeper into each factor affecting CO2 laser cutting machines’ performance when working with acrylic materials. By offering detailed insights into each aspect that contributes to successful outcomes in this field, operators can better understand how to optimize their processes effectively.