1. Laser Power
The power of the laser is a critical factor in CO2 laser cutting. Higher power settings allow for cutting thicker materials and achieving faster cutting speeds. However, excessive power can lead to melting and poor edge quality, while insufficient power may result in incomplete cuts and rough edges.
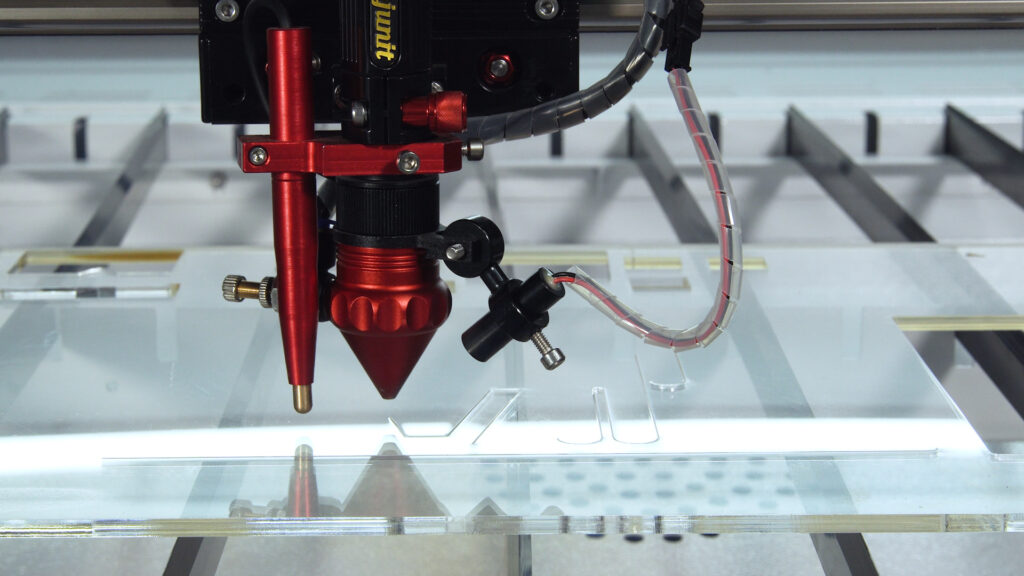
2. Cutting Speed
Cutting speed is directly proportional to the laser power density and inversely proportional to the material’s density and thickness. Optimal cutting speed ensures clean cuts and high efficiency. Too fast a speed can cause incomplete cuts, while too slow a speed can lead to excessive melting and rough edges.
3. Focus Position
The position of the laser focus relative to the workpiece surface is crucial for achieving high-quality cuts. Typically, the focus is set just on or slightly below the workpiece surface. Proper focus ensures a small spot size and high power density, which are essential for precise cutting.
4. Assist Gas Pressure
Assist gases like oxygen, nitrogen, or compressed air are used to blow away molten material and prevent oxidation. The pressure of the assist gas must be optimized based on the material and thickness. High pressure is needed for thin materials to prevent slag, while lower pressure is better for thicker materials to avoid frosting.
5. Beam Quality
The quality of the laser beam, often measured by the Beam Parameter Product (BPP), affects the smoothness and precision of the cut. A lower BPP value indicates a higher quality beam, which results in finer cuts and higher accuracy.
6. Material Type and Thickness
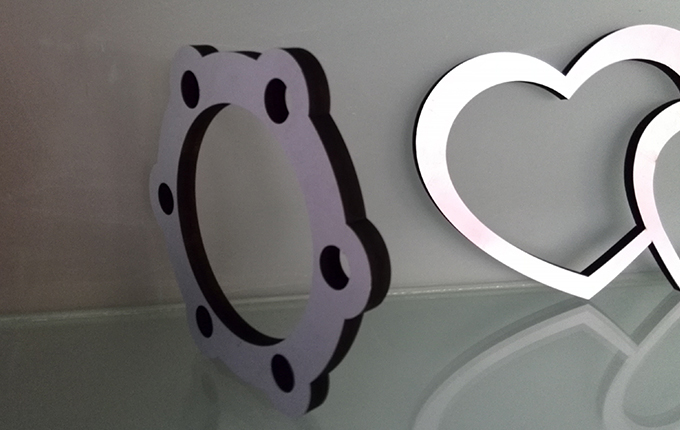
Different materials absorb and conduct heat differently, affecting how they respond to laser cutting. Metals, plastics, and organic materials each have unique cutting characteristics. Thicker materials generally require higher power and slower cutting speeds.
7. Cutting Environment
The ambient temperature, humidity, and cleanliness of the cutting environment can impact the performance of the CO2 laser cutter. Proper machine calibration and maintenance are essential to ensure consistent cutting quality.
8. Optical System
The condition and alignment of the optical components, such as lenses and mirrors, are vital for maintaining beam quality. Contaminated or misaligned optics can lead to poor cutting performance and reduced efficiency.
9. Pulse Frequency
For pulsed CO2 lasers, the pulse frequency affects the cutting speed and edge roughness. Higher frequencies are necessary for high-speed cutting, while lower frequencies may be used for thicker materials to ensure deeper penetration.
10. Nozzle Design
The design and condition of the cutting nozzle influence the flow of assist gas and the quality of the cut. A well-maintained nozzle with the correct diameter and alignment ensures efficient removal of molten material and prevents contamination of the lens.By understanding and optimizing these factors, operators can achieve high-quality cuts with CO2 laser cutting technology, ensuring efficiency and precision in various industrial applications.