The True Cost of Owning a Laser Cutter: A Comprehensive Analysis
Laser cutting technology has revolutionized manufacturing and fabrication processes across many industries. However, the decision to invest in a laser cutter requires careful consideration of both upfront and ongoing costs. This article provides a detailed breakdown of the expenses associated with owning and operating laser cutting machines, focusing on the two main types: CO2 and fiber lasers.
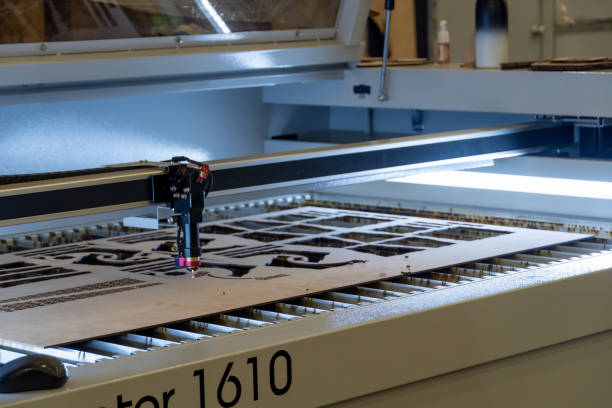
Initial Investment
The upfront cost of purchasing a laser cutter varies significantly based on the type, power, and capabilities of the machine:CO2 Lasers:
- Entry-level machines: $8,000 – $50,000
- Power range: 100W – 500W
- Best suited for cutting non-metals and thin metals
Fiber Lasers:
- Industrial-grade machines: $250,000 – $2,000,000+
- Power range: 1kW – 20kW
- Capable of cutting thick metals with high precision
Key factors affecting initial costs include:
- Cutting bed size
- Automation features
- Brand reputation
- Additional options (e.g. rotary attachments, fume extraction)
Operational Costs
- Labor Costs
- CO2 lasers: Often require only one operator
- Fiber lasers: Ideally operated by a team of 2-3 staff
- Operator
- Materials handler
- Parts handler
- Multiple shifts may be necessary for 24/7 operation to maximize ROI
- Energy Consumption
- Fiber lasers: More energy-efficient, converting up to 30-40% of input power into laser energy
- CO2 lasers: Less efficient, typically converting only 10-15% of input power
- Assist Gases
- Nitrogen or oxygen used to improve cut quality and prevent oxidation
- Costs can range from $3,000 – $30,000 per month for high-volume operations
- On-site gas generation systems can help reduce long-term costs
- Maintenance and Consumables
CO2 Lasers:
- Distilled water changes (every 100 hours)
- X/Y axis lubrication
- Daily alignment adjustments
- Laser tube replacement: $700-$4,000 every 2,000-5,000 hours
Fiber Lasers:
- Daily lens and nozzle alignment
- Lens savers: $10-$20 each, replaced daily
- Sacrificial slats: $1-1.50 per pound, replaced every 2-3 days to monthly
- Air/gas filters: $2,000 – $4,000, replaced semi-annually
- Dust collector filters: $800 – $2,000, replaced every 6 months
- Material Costs
- Raw material expenses vary based on type and quality
- Material utilization efficiency: 50-90% depending on part geometry and nesting
- Storage costs for raw materials and finished parts
Hidden Costs to Consider
- Training and Skill Development
- Initial operator training
- Ongoing education for software updates and new techniques
- Software and Design Costs
- CAD/CAM software licenses
- Regular software updates
- Facility Modifications
- Proper ventilation systems
- Electrical upgrades
- Climate control for sensitive components
- Insurance
- Equipment insurance
- Liability coverage for potential accidents
- Downtime and Repairs
- Lost productivity during maintenance or unexpected breakdowns
- Costs of emergency repairs and replacement parts
Return on Investment (ROI) Considerations
To maximize ROI:
- Aim for high utilization rates, ideally 24/7 operation for fiber lasers
- Optimize part nesting to improve material efficiency
- Invest in automation to reduce labor costs and increase throughput
- Regularly maintain equipment to prevent costly breakdowns
- Stay updated on latest technologies to remain competitive
Conclusion
While the initial investment in a laser cutter can be substantial, particularly for high-powered fiber lasers, the long-term benefits often outweigh the costs for many businesses. CO2 lasers offer a lower entry point and are suitable for diverse materials, while fiber lasers provide superior speed and precision for metal cutting.When considering a laser cutter purchase, it’s crucial to conduct a thorough cost-benefit analysis based on your specific production needs, expected volume, and available resources. Factor in both obvious and hidden costs to get a true picture of the total cost of ownership. With proper planning and management, a laser cutter can become a valuable asset that drives efficiency, quality, and profitability in your manufacturing operations.