When comparing CO2 laser cutting and waterjet cutting, several key factors need to be considered, including the types of materials each method can handle, precision, speed, environmental impact, and cost. Here is a detailed comparison of these two cutting technologies:
Material Compatibility
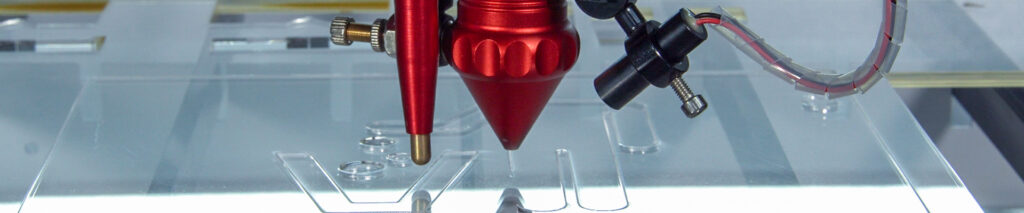
- CO2 Laser Cutting: This method is highly effective for cutting a variety of materials, including metals (such as stainless steel and aluminum), plastics, wood, and fabrics. However, it is generally more suitable for thinner materials, typically up to 0.4 inches (10 mm) thick.
- Waterjet Cutting: Waterjet cutting can handle a broader range of materials, including thick and dense materials like stone, ceramics, and metals. It can cut materials up to 2 inches (50 mm) thick or more, making it ideal for applications requiring the cutting of very thick materials.
Precision and Quality
- CO2 Laser Cutting: Laser cutting is known for its high precision and ability to create intricate designs. The minimum cut size for laser cutting is around 0.006 inches (0.15 mm), which allows for very detailed and precise cuts. Additionally, laser cutting produces clean edges with minimal post-processing required.
- Waterjet Cutting: While waterjet cutting is precise, it is generally less precise than laser cutting, with a minimum cut size of around 0.02 inches (0.5 mm). The process can leave a sandblasted appearance on the cut surface, and some cleanup may be required due to the abrasive materials used.
Speed
- CO2 Laser Cutting: Laser cutting is typically faster than waterjet cutting, especially for thinner materials. Cutting speeds can range from 20 to 70 inches per minute (ipm), and high-power lasers can cut even faster.
- Waterjet Cutting: Waterjet cutting is slower, with speeds ranging from 1 to 20 ipm, depending on the material and thickness. The process is generally slower due to the erosion mechanism used to cut through materials.
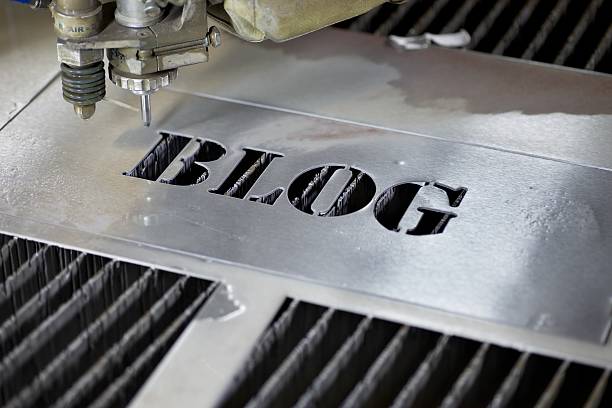
Environmental Impact
- CO2 Laser Cutting: Laser cutting can produce toxic fumes, especially when cutting plastics and certain metals, which necessitates proper ventilation and safety measures. However, it generates less physical waste compared to waterjet cutting.
- Waterjet Cutting: Waterjet cutting is considered more environmentally friendly in terms of not producing toxic fumes. However, it generates significant waste in the form of used water and abrasives, which require proper disposal.
Cost
- CO2 Laser Cutting: Laser cutting equipment is generally less expensive than waterjet cutting equipment. Operating costs are also lower due to the faster cutting speeds and lower maintenance requirements.
- Waterjet Cutting: Waterjet cutting is more expensive due to the higher cost of equipment and the need for abrasives. Additionally, the slower cutting speeds can increase labor costs.
Safety
- CO2 Laser Cutting: Laser cutting is relatively safe, but it requires proper ventilation to handle fumes and dust. Safety goggles are recommended to protect against laser exposure.
- Waterjet Cutting: Waterjet cutting involves high-pressure water and abrasives, which can be hazardous. Operators need to wear protective gear, including goggles and ear protection, due to the noise and potential for injury from the high-pressure jet.
Applications
- CO2 Laser Cutting: Ideal for applications requiring high precision and intricate designs, such as electronics, automotive parts, and decorative items. It is also suitable for engraving and etching.
- Waterjet Cutting: Best suited for cutting thick, dense materials and applications where heat-affected zones must be avoided, such as in aerospace and heavy machinery.
In summary, the choice between CO2 laser cutting and waterjet cutting depends on the specific requirements of the project, including material type and thickness, precision needs, speed, environmental considerations, and budget. Each method has its strengths and is better suited for different applications.