Laser cutting has been widely used in modern industry due to its advantages such as wide range of cutting materials, fast cutting speed, narrow slit, good cutting quality, small heat-affected zone, and high processing flexibility. Laser cutting technology has also become one of the most important laser processing technologies. One of the most mature technologies. Among low- and medium-power cutting machines, CO2 lasers account for the vast majority. Acrylic board is a polymethylmethacrylate board, also called PMMA. It is a highly plastic molecular material with good transparency, chemical stability and weather resistance. It is easy to dye, easy to process, and has beautiful appearance. It can be laser cut. Excellent performance. The author has realized while guiding undergraduate students to participate in mechanical competitions and project practice. If you want to quickly make the mechanism designed in the drawing into a physical prototype, you can use the following method: when designing the drawing, all use the form of splicing plates. Use computer graphics software to layout according to different plate thicknesses, input the layout pattern into the CO2 laser cutting machine, cut acrylic plates of different thicknesses, and then assemble the cut acrylic plate parts through bonding or bolting. You can create a prototype. Compared with traditional mechanical processing (turning, milling, planing, grinding, drilling, etc.), this method greatly shortens the manufacturing time of the prototype and is convenient and easy to use. This article introduces the method and application of CO2 laser cutting of acrylic sheets.
1 Structural design of acrylic parts for laser cutting
1) The edges of the parts that need to be spliced are designed to be concave and convex in a zigzag shape to facilitate positioning and expand the area of adhesive contact during splicing, as shown in the picture.
2) The thickness of acrylic sheets commonly used for structural parts is 3 mm, 5 mm, 6 mm, 8 mm, 10 mm, and 12 mm. It is recommended to use acrylic plates with a thickness of 3 mm and 6 mm to complete the design. Appropriately increase the rib plate support to improve the stiffness of the prototype (as shown in the picture), rather than just increasing the thickness of the acrylic plate to increase the stiffness and avoid material waste. Acrylic plates with thicknesses of 3 mm and 6 mm are more cost-effective, and the thicker the plate, the greater its weight. Sometimes choosing a plate that is too thick will reduce the stiffness of the prototype due to its excessive weight.
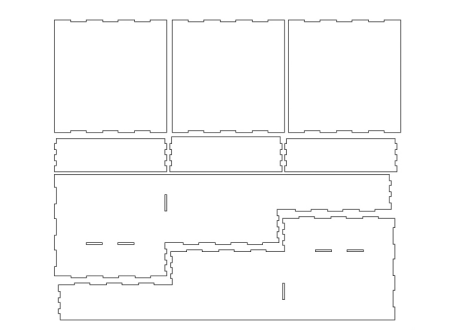
3) When designing a circular hole in a part, the recommended value of the diameter d of the circular hole is d≥0.8D.
(1) In the formula, D is the thickness of the plate, D≤12 mm. If the round hole is designed too small and the plate thickness is large, the cutting quality of the round hole will be poor. A CO2 laser with a maximum output power of 120 W was used to cut a hole with a diameter of 3 mm on an acrylic plate with a thickness of 12 mm. After constantly adjusting the cutting speed and cutting energy, satisfactory cutting quality could not be achieved, and round holes appeared. Problems such as deformation and molten material at the bottom of the round hole can be achieved by expanding the diameter of the round hole to 10 mm to achieve more satisfactory cutting quality. The reason for this phenomenon is that during the laser cutting process, the laser energy is transferred from the upper surface of the plate to the bottom. When the plate is thin, the energy transfer is faster, and the materials located on the upper surface and bottom of the plate All can absorb enough energy almost simultaneously and vaporize instantly; when the plate is thick and small holes need to be cut, the material on the upper surface of the plate has enough energy to vaporize directly, but the time for the plate on the bottom to absorb energy is longer than that on the upper surface. The long surface and the cutting of small holes cause heat to accumulate in a small local area. The acrylic at the bottom does not have time to vaporize, but liquefies, becoming a molten substance and remaining at the edge of the bottom.
2. Optimize the layout of the pattern before laser cutting to improve the utilization rate of acrylic sheet material.
1) The distance between the parts should be as narrow as possible, and try to layout as many parts as possible in one format, but the parts should not be arranged too closely. , otherwise the heat-affected zone during laser cutting will affect the nearby parts to be cut. The recommended value of distance L between parts is L=k·D. In the formula: D is the thickness of the plate, D≤12 mm; the value range of k is 0.25~0.5. The value of k becomes smaller as the plate increases and is adjusted according to the specific cutting situation. Generally, the plate is a 3 mm plate, and the distance between parts is 1.5 mm, as shown in the picture.
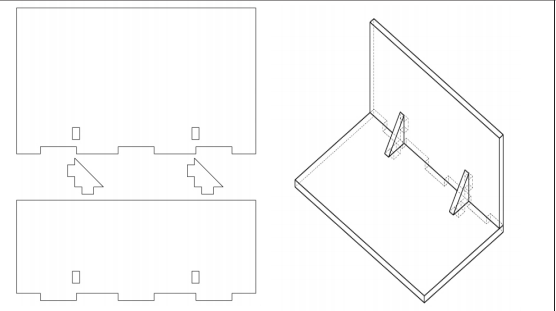
2) Small parts and large parts are put together for nesting and cutting. In the manufacture of prototypes, there are definitely parts of different sizes. Due to the characteristics of the parts themselves, material needs to be removed from the interior of many large parts. If the small parts are placed as close as possible to the places where the large parts are to be cut, the utilization rate of the acrylic plate can be greatly improved. As shown in picture.
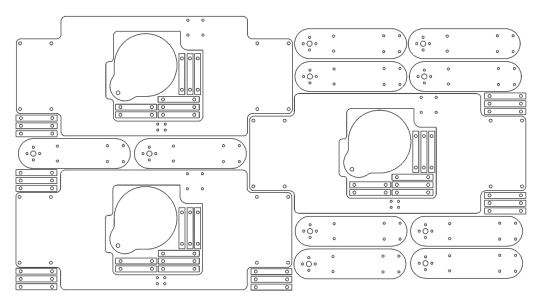
3) When cutting very regular parts, such as rectangles, triangles, etc., you can use collinear layout so that the edges of the parts share a line. When cutting, you only need to make one pass to cut two edges at the same time, reducing the number of passes. The number of cuts also reduces the distance between parts to zero, saving materials and processing time. As shown in picture. However, collinear layout also has its own shortcomings, that is, as the thickness of the cutting plate increases, the cutting quality will decrease. This is because as the thickness of the plate increases, the width of the slit will increase. The board thickness recommended here for collinear typesetting is ≤6 mm.
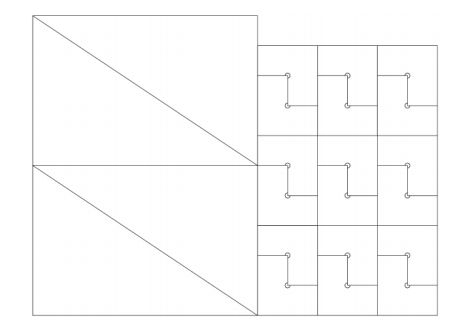
3. Acrylic plate cutting parameter settings
There are two main settings for cutting parameters: cutting speed and cutting energy. The two need to work well together to produce good cutting quality. Laser cutting can cut through the acrylic plate, that is, the plate absorbs enough energy to vaporize within a unit time. The cooperation of these two parameters generally has the following two ideas: 1) low cutting power, slow cutting speed; 2) High cutting power, high cutting speed. If you adopt the first cutting idea, the plate can be cut through. However, when this cutting parameter is adopted, the heat will accumulate locally for too long, resulting in an increase in the heat-affected zone, poor cutting quality, and it is easy to Produce a melt. Therefore, the second cutting idea is recommended here. As long as the power of the cutting machine allows, adjust the cutting power to the highest possible level (since the maximum allowable values of laser generators produced by various manufacturers are different, refer to the recommended values provided by the manufacturers. ), then adjust the cutting speed and try cutting from a high speed. If the speed is too fast, it cannot cut through the plate. It is better to adjust it to a speed that can cut through the plate.
4 Glue selection for bonding acrylic sheets
Cut acrylic sheet parts are generally bonded together with glue to form an assembly. There are many glues to choose from on the market. It is recommended to use acrylic-specific glue instead of the all-purpose 502 glue or AB glue. Special glue for acrylic uses a solvent-based adhesive. Its bonding principle relies on corroding the surface of acrylic to fuse the two surfaces together, so the bonding surface after bonding with this kind of glue is very strong. It is very important to choose the right glue for acrylic plate bonding, because most of the cut parts are bonded together by glue. If the bonding strength is poor, it will affect the strength of the entire component.