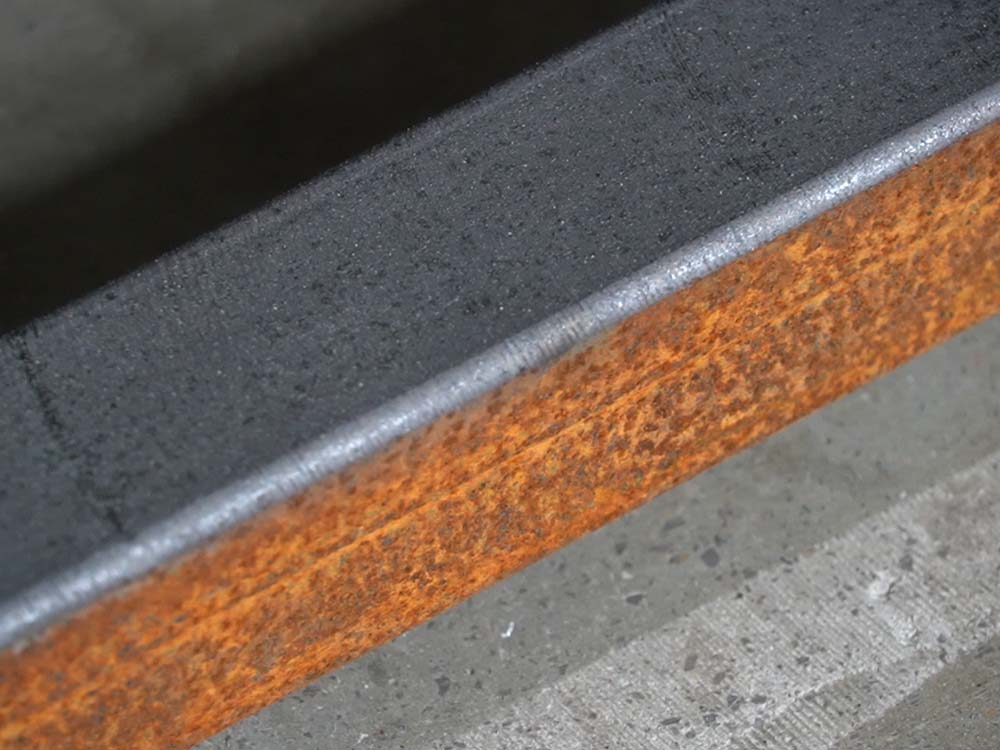
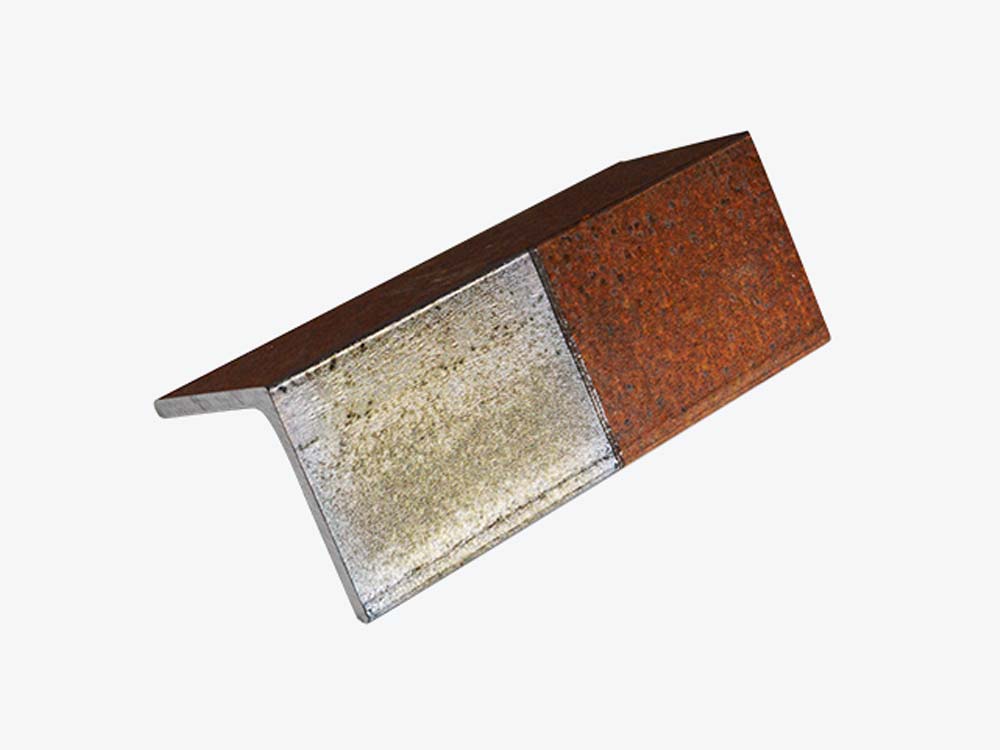
Laser rust removal is an innovative and efficient method used to clean metal surfaces, particularly those affected by rust and other contaminants. This technology leverages the power of laser beams to ablate rust without damaging the underlying material, making it a preferred choice across various industries. The applications of laser rust removal are diverse, ranging from automotive and aerospace to historical artifact preservation.
How Laser Rust Removal Works
Laser rust removal operates on the principle of laser ablation, where a high-energy laser beam is focused onto the rusted surface. The laser heats the rust to its evaporation point, causing it to vaporize without affecting the base material. This process is highly efficient and environmentally friendly, as it eliminates the need for harsh chemicals or abrasive materials traditionally used in rust removal.
Key Applications of Laser Rust Removal
Automotive Industry
In the automotive sector, laser rust removal plays a crucial role in maintaining and restoring vehicle components. Rust can significantly weaken structural integrity and lead to costly repairs if not addressed promptly. Laser cleaning systems are employed to remove rust from chassis parts, engine components, and other critical areas without damaging the underlying metal.The precision of laser rust removal allows for targeted cleaning in intricate areas where traditional methods may struggle. For example, laser systems can effectively clean the tight spaces between components or around welds, ensuring that every part of the vehicle is free from corrosive materials. This not only enhances the appearance of vehicles but also prolongs their lifespan by preventing further corrosion and degradation.
Aerospace Industry
The aerospace industry demands the highest standards of safety and performance, making laser rust removal an invaluable tool. Components such as turbine blades and fuselage parts must be meticulously cleaned to ensure optimal performance under extreme conditions. Laser cleaning effectively removes rust and contaminants without compromising the integrity of lightweight materials used in aircraft construction.In aerospace applications, where weight reduction is critical, laser rust removal provides a non-invasive solution that maintains the structural integrity of components. By eliminating rust without harsh chemicals or abrasive methods, manufacturers can ensure that their parts meet stringent safety regulations while enhancing overall performance.
Manufacturing and Heavy Industry
Within manufacturing and heavy industry, laser rust removal is utilized for cleaning tools, molds, and machinery parts that are prone to rust due to exposure to moisture and other corrosive elements. Traditional methods like sandblasting can be time-consuming and may damage delicate equipment; however, laser cleaning offers a precise alternative that minimizes wear on tools while effectively removing rust.By implementing laser rust removal technologies, manufacturers can maintain their equipment in peak condition, reducing downtime associated with maintenance and repairs. The efficiency of this method allows for quick turnaround times in production environments where time is critical, ultimately leading to cost savings and improved operational efficiency.
Marine Applications
The maritime industry faces significant challenges related to corrosion due to saltwater exposure. Laser rust removal is particularly beneficial for cleaning ship hulls, propellers, and other components that suffer from marine corrosion. This method ensures that surfaces are adequately prepared for repainting or protective coatings without introducing contaminants that could lead to further corrosion.In addition to removing rust, laser cleaning can also eliminate barnacles and other marine organisms that attach themselves to underwater surfaces. By maintaining clean surfaces on vessels, operators can improve fuel efficiency and reduce maintenance costs associated with marine growth.
Historical Artifact Preservation
Museums and conservationists increasingly employ laser rust removal techniques for cleaning historical artifacts made of metal without damaging their surfaces. This non-invasive method preserves the integrity of delicate items while effectively removing layers of rust and grime accumulated over time.For example, when restoring antique machinery or historical weapons, conservators must ensure that the original materials are not compromised during the cleaning process. Laser rust removal provides a controlled environment where only the unwanted contaminants are removed, allowing artifacts to be preserved for future generations while maintaining their historical significance.
Advantages of Laser Rust Removal
- Environmentally Friendly: Unlike traditional methods that often rely on chemicals or abrasive materials, laser rust removal produces minimal waste and does not require harmful substances. This makes it a greener alternative that aligns with modern environmental standards.
- Precision Cleaning: The focused nature of lasers allows for precise cleaning in hard-to-reach areas or intricate geometries. This capability is particularly valuable in applications where maintaining the integrity of surrounding materials is critical.
- Cost-Effective: Although the initial investment in laser equipment can be significant, the long-term savings associated with reduced maintenance costs and increased equipment lifespan make it a cost-effective solution for many industries.
- Reduced Labor Costs: Laser rust removal systems can be automated or semi-automated, significantly reducing labor costs associated with manual cleaning methods. Operators can set up machines to perform cleaning tasks efficiently without extensive manual intervention.
Challenges and Considerations
While laser rust removal offers numerous advantages, there are some challenges and considerations:
- Initial Investment: The cost of purchasing and maintaining laser cleaning equipment can be high compared to traditional methods. However, many businesses find that the long-term benefits outweigh these initial costs.
- Training Requirements: Operators may require specialized training to effectively use laser cleaning machines safely and efficiently. Understanding how to adjust parameters such as power settings and pulse duration is crucial for optimal results.
- Material Limitations: Although lasers are effective on many metals, certain materials may not respond well to laser cleaning due to their thermal properties. It’s essential to evaluate material compatibility before implementing this technology.
Conclusion
Laser rust removal represents a significant advancement in surface cleaning technology, offering efficient, precise, and environmentally friendly solutions across various industries. Its applications span automotive manufacturing, aerospace engineering, marine maintenance, historical preservation, and more. By understanding its benefits and challenges, businesses can make informed decisions about integrating laser cleaning technology into their operations for enhanced performance and sustainability.