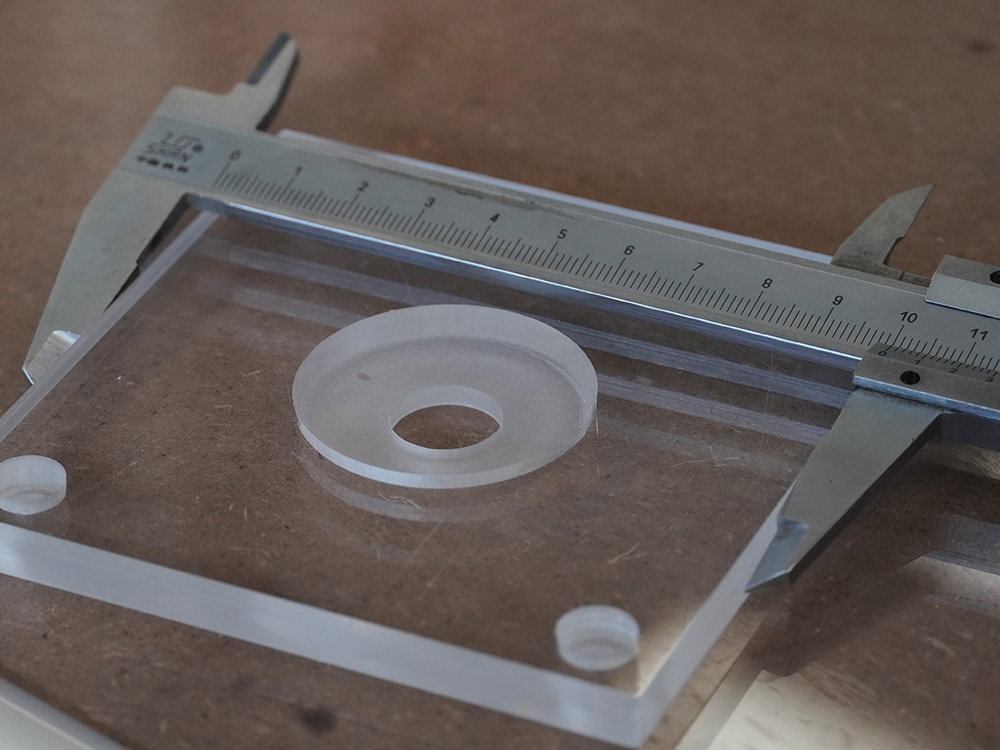
Introduction to CO2 Laser Cutting of Acrylic
CO2 lasers are widely used for cutting and engraving acrylic (polymethyl methacrylate or PMMA) due to their ability to produce high-quality cuts with polished edges. The 10.6 micrometer wavelength of CO2 lasers is readily absorbed by acrylic, allowing efficient melting and vaporization of the material.
Advantages of Laser Cutting Acrylic
- Precision Cutting: Laser cutting provides extremely precise and intricate cutting capabilities for acrylic, enabling complex designs and patterns.
- Polished Edges: The laser melts and vaporizes the acrylic, resulting in smooth, polished edges without the need for secondary finishing operations.
- No Tool Wear: Unlike mechanical cutting tools, lasers do not experience wear, ensuring consistent cut quality over time.
- Minimal Material Deformation: Laser cutting generates very little mechanical stress on the acrylic, minimizing warping or deformation of the material.
- Versatility: CO2 lasers can cut a wide range of acrylic thicknesses, from thin sheets to thick slabs, making them suitable for various applications.
Types of Acrylic for Laser Cutting
There are two main types of acrylic used for laser cutting:
- Cast Acrylic: Produced by pouring liquid acrylic into molds, cast acrylic has excellent optical properties and is ideal for engraving applications. However, it may have slight thickness variations across the sheet.
- Extruded Acrylic: Formed by extruding molten acrylic through a die, extruded acrylic has consistent thickness and is well-suited for cutting applications that require precise fitting of parts.
Laser Cutting Parameters for Acrylic
The optimal laser cutting parameters for acrylic depend on factors such as thickness, color, and desired cutting speed. Here are some general guidelines:
- Power: Higher power settings (e.g., 50-100% of maximum power) are typically used for cutting acrylic to ensure complete melting and vaporization.
- Speed: Slower cutting speeds (e.g., 10-30 mm/s) are recommended for thicker acrylic sheets to allow sufficient energy transfer and produce clean cuts.
- Frequency: A higher pulse frequency (e.g., 5,000-20,000 Hz) helps achieve smooth, uniform cuts by evenly distributing the energy input.
- Focus: The laser beam should be focused precisely on the surface of the acrylic for optimal cutting results.
- Assist Gas: Using an air or gas assist can help remove molten material from the cut kerf, improving cut quality and reducing residue buildup.
Applications of Laser Cut Acrylic
Laser-cut acrylic finds applications in various industries due to its versatility, optical clarity, and ability to produce intricate designs. Some common applications include:
- Signage and displays
- Architectural models and prototypes
- Awards and trophies
- Lighting fixtures and light guides
- Jewelry and fashion accessories
- Product packaging and point-of-purchase displays
- Scientific and medical equipment
Safety Considerations
While acrylic is generally considered a safe material for laser cutting, proper ventilation and safety precautions are still necessary:
- Use a fume extraction system to remove vapors and particles generated during cutting.
- Wear appropriate personal protective equipment (PPE), such as safety glasses and a respirator, if necessary.
- Ensure the laser cutting area is clear of flammable materials, as acrylic can produce localized flames during cutting.
- Follow all manufacturer guidelines and safety protocols for operating the laser cutting system.
By understanding the principles, parameters, and safety considerations of CO2 laser cutting of acrylic, manufacturers can leverage this technology to produce high-quality, intricate acrylic components and products efficiently and cost-effectively.